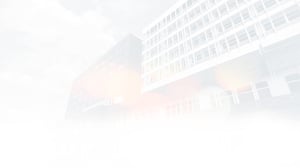
Innovation at the center of CMU
CMU in Geneva poses a huge challenge, as stakeholders need to work in an occupied site and have the ability to manage data at all stages of the building's lifecycle.
102,000 sqm
3008
Electrical renovation
swissBIM
OCBA
DEPLANTA
MDS
BG
SUCCESS STORY
In the heart of the Canton of Geneva, the University Medical Center is in the middle of a huge electrical renovation project. The company SWISSBIM was chosen to manage this ambitious project. The challenge is great because it is necessary to be able to work in an occupied site and to have the capacity to manage the data at all stages of the building's life cycle. In this project, it is the BIM I that is at the heart of the process. Indeed, it is necessary to be able to collect, analyze and sort all the building's electrical data so that it can be used in the Operation and Maintenance Management phase. Its main actors, Dylan MARTINS, director and Emré AKKAIA, BIM project manager, explain the challenges, their approach and their vision.
1. CAN YOU DESCRIBE YOUR PROJECT?
DYLAN MARTINS: The project involves an occupied site renovation of the CMU. The work began in 2020 and will continue until 2024. The renovation specifically concerns the electrical part of the CMU, including the upgrading of certain elements such as airlocks, cabinets, etc. The total surface area of the project is 102,000 m².
It should be noted that the project is a hybrid one, as we are currently in the execution phase, but the operating approach is also at the heart of our concerns, as the building continues to live. The fact that we are on an occupied site and that the services offered will be maintained requires agility and flexibility in the management of this project.
In terms of the team, we have different players. The client is OCBA, the architect is DEPLANTA, the general contractor is MDS (its mission is to manage the works), the electrical engineer is BG, the operator is the University of Geneva. SWISSBIM's mandate covers the entire project management in BIM, from BIM project management, to BIM coordination to BIM management, including data management.
2. WHEN WAS DROFUS FIRST USED? AT WHAT STAGE OF THE PROJECT?
DYLAN MARTINS: The solution was implemented in the summer of 2021, a little over a year ago. The project was in the design stage at that time. Since the client wanted to use dRofus for the operation of the building, the solution was implemented on the project early enough to be able to manage the data upstream. One of the objectives was to be able to list the existing CMU data in order to carry out a complete inventory. We needed to have all the data and associated information in one place. This notion of centralized data was essential to avoid the situation where each person (or stakeholder) had his own database with different information and different naming rules. Then, things evolved and our customer saw the potential of dRofus to optimize the management of this data in the operational phase. This is how the installation of electrical systems and the integration of the final data in the QR code quickly came into play in order to keep this database alive throughout the building's lifecycle.
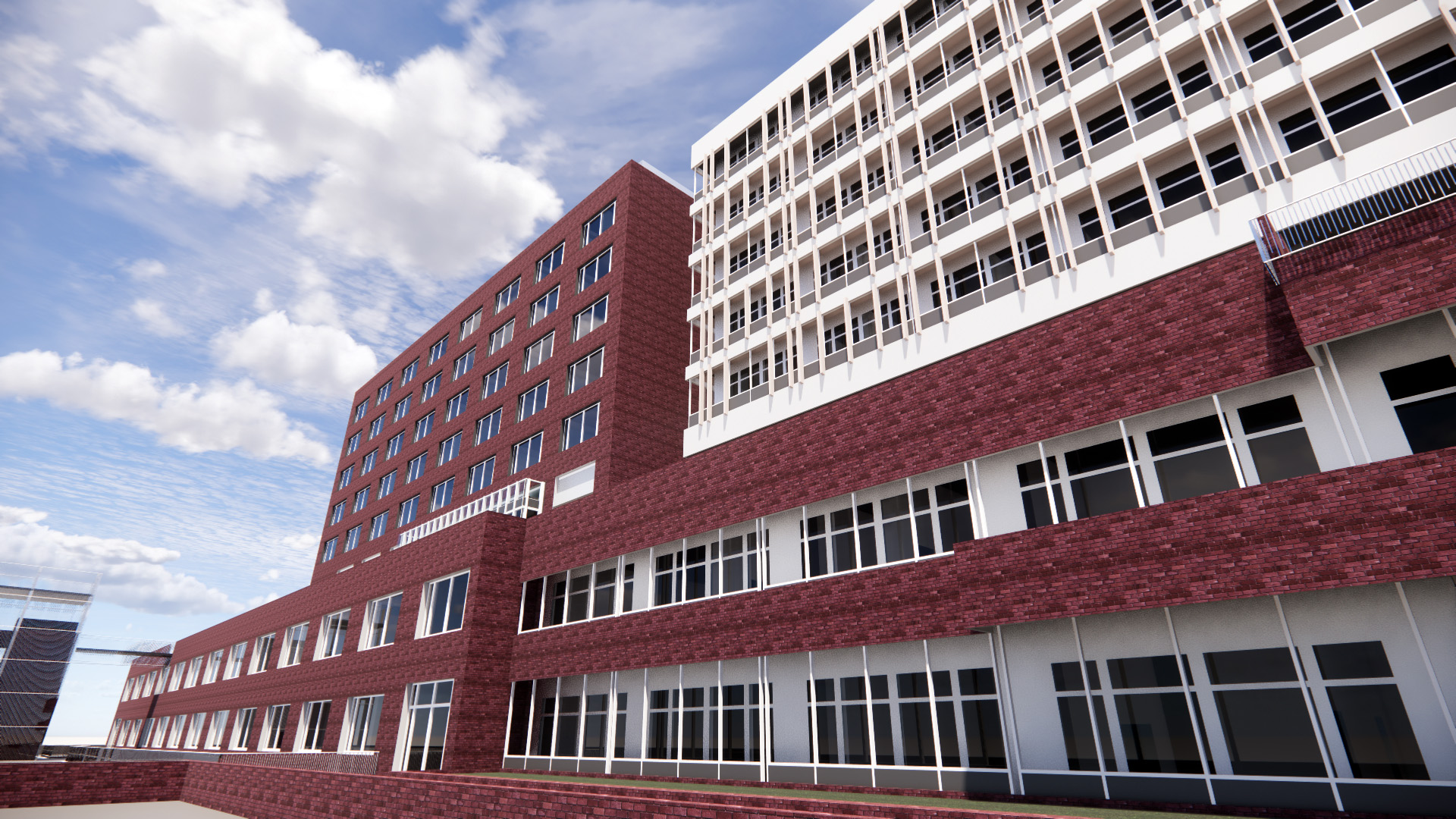
3. WHAT WERE THE MAIN REASONS FOR USING DROFUS ON YOUR PROJECT?
DYLAN MARTINS: dRofus allowed us to implement several use cases. Firstly, to take stock of all the equipment with their degree of maintenance of ELEC function, because we needed to be able to compensate for a power cut, for example. This clearly allowed us to optimize the management of the equipment on this specific project because we were in an occupied site. Then, we were able to create a "power" parameter for the equipment, so that the electrician could size his emergency panel.
dRofus also clearly allowed us to work collaboratively thanks to the synchronization with the digital model. Before using dRofus, we clearly could not anticipate and the data was not managed at all. The tool has really allowed us to be operationally efficient. Of course, Excel could allow us to move forward, but not as quickly.
In addition, the QR codes from dRofus web installed on each new electrical panel were intended to make the panel builder's life easier. In concrete terms, it is important to understand that dRofus is useful at all stages of the project and building life cycle: design to identify and size them, execution to install them and, of course, in the operating phase. The benefit is therefore total for our project.
There is also the question of inventory management, but we have not yet made use of this use case to its full extent.
To date, we are working with 4 ARCHI models, 1 ELEC/MCR model, 1 HVAC model and a "chilled water" model that are all connected to dRofus. All the models of the project were made with REVIT. In addition, we used APIs to have all our parts updated in our EXCEL, which avoids us having to export. This allows a real-time update in EXCEL of the data implemented in dRofus.
To read the full case study download the PDF
CHALLENGES
- Relatively low budget for design, implementation and marketing
- 8-week time constraint for the whole project
- Website must match existing digital corporate identity
- Website should be deeply integrated into the HubSpot solution
- Design & development from scratch is not feasible
- Customer would like to be able to edit content and structure
- Website must be implemented in three languages
- Webdesign must match modern design standards
RESULTS
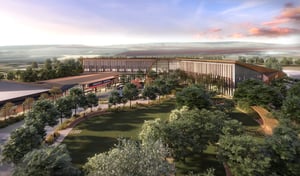
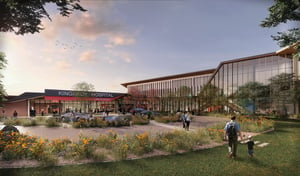
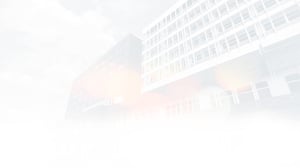
“Thanks to dRofus, we have considerably reduced the amount of exchanges between project teams, and we limit the errors and loss of information related to these exchanges. We now have a single platform that centralizes the data and all our technical documentation. We have created a bridge between the project and operations by linking the project/operations teams"
“dRofus is the operating reference for the building"
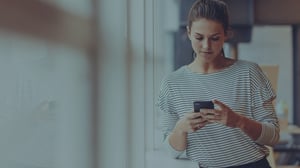